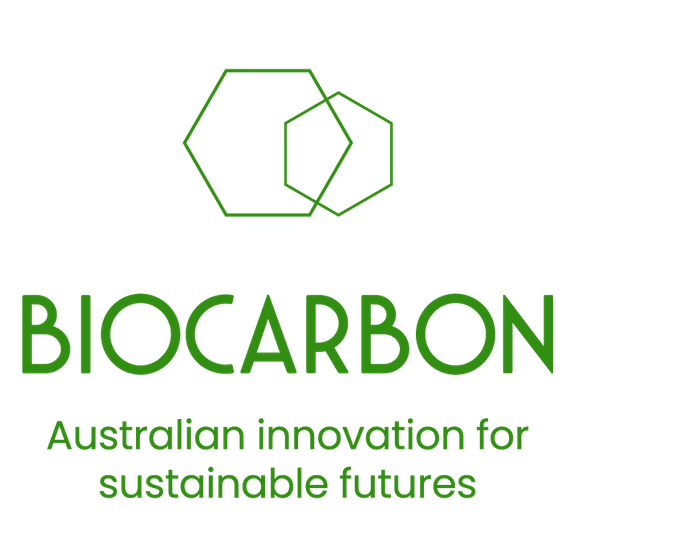
Steelmaking accounts for approximately 8% of the worldâs greenhouse gas emissions (GHGs) and is commonly labelled a hard-to-abate sector. Typically, steel is produced via one of two methods:
- Blast Furnace, using iron ore and coke.
- Electric Arc Furnace, using iron or scrap steel.
The Blast Furnace (BF) Process
The BF process consumes approximately 700kg of coal for every tonne of steel produced, with 70% of the worldâs steel being produced this way. This method is responsible for the majority of steelmakingâs GHG emissions. The steel industry aims to replace the BF process with direct reduced iron (DRI), using green hydrogen instead of carbon when it becomes commercially available at a viable price. DRI technology is mature, and large plants already use natural gas instead of hydrogen to produce iron. However, iron produced by the hydrogen DRI technique still requires processing in an EAF, which uses coke to make steel.
The Electric Arc Furnace (EAF) Process
The EAF process has relatively low emissions compared to the BF, especially when powered by green electricity. The EAF uses about 15kg of higher-grade coke per tonne of steel produced, making it a much lower emitter. However, to achieve net-zero emissions, this coke must be eliminated from the process.
Charcoal as a Solution
Charcoal, made by heating biomass such as wood chips in a low-oxygen environment (a process known as pyrolysis), offers a potential solution. This method was common in the early 1900s. When processed correctly, charcoal has a higher carbon content and lower ash compared to fossil coke. However, it lacks certain physical qualities required for the EAF process.
Historically, all steel was made using charcoal, and this is still the case in mini BFs in Brazil. However, using charcoal in large modern BFs is challenging because it lacks the required strength. Australian and European steelmakers have experimented with small percentages of charcoal in blast furnaces with some success. For instance, one large European steelmaker has commissioned a pyrolysis plant to substitute a small percentage of coal with charcoal.
Many industries and metal refining processes (such as ferro alloys, copper and zinc) use coke as a reducing agent. Like steel these industries will require a replacement for coke in order to decarbonise. BioCarbon have begun discussions with significant non steel metal producers to tailor a carbon solution to their needs.
Charcoal is considered net-zero because carbon in the source biomass is extracted from the atmosphere by plants via photosynthesis, unlike coke, which adds additional carbon into the atmosphere from coal. When charcoal is used in steelmaking, the carbon is emitted back to the atmosphere as CO2, but itâs net-zero because thatâs where the carbon originated. There is also a growing voluntary market in biochar projects, which incorporate charcoal into the soil, thereby removing it from the atmosphere.
BioCarbon's Innovations
BioCarbon is an Australian climate tech startup dedicated to producing renewable carbon products from low-value biomass using advanced manufacturing technologies. Their products include biochar, pyroligneous acid, bio oil, and syngas, which are used in industrial and agricultural applications.Â
BioCarbon has developed two key technologies that will enable the steel industry to eliminate coke from EAF steelmaking:
- An economical pyrolysis process for making high-carbon charcoal,
- A process for converting charcoal into âGreenChar Carbon.â
Key Technologies and Achievements:
- Renewable Carbon for Steelmaking: BioCarbon has developed a cost-effective pyrolysis process to produce high-carbon charcoal and convert it into "GreenChar Carbon."Â
- Government Support: BioCarbon has received Australian Government support, highlighting their contribution to green steelmaking and CO2 abatement.
- Commercial Collaborations: They collaborate with Infrabuild and other partners to demonstrate the benefits of their renewable carbon products to domestic and international steelmakers.
Environmental Impact
- CO2 Abatement: BioCarbonâs products significantly reduce CO2 emissions and will provide carbon credits for offsetting business carbon footprints.
- Regenerative Agriculture: They manufacture pyroligneous acid which allows a reduction in synthetic chemical use and are developing carbon-rich fertilisers, and carbon-based feed additives.
BioCarbon is advancing sustainable practices and creating additional revenue streams for their partners, positioning themselves as leaders in the transition to greener industrial processes.
BioCarbonâs GreenChar Carbon innovation has successfully replaced 100% of charge coke in Electric Arc Furnaces during trials, producing around 3,000 tonnes of steel.
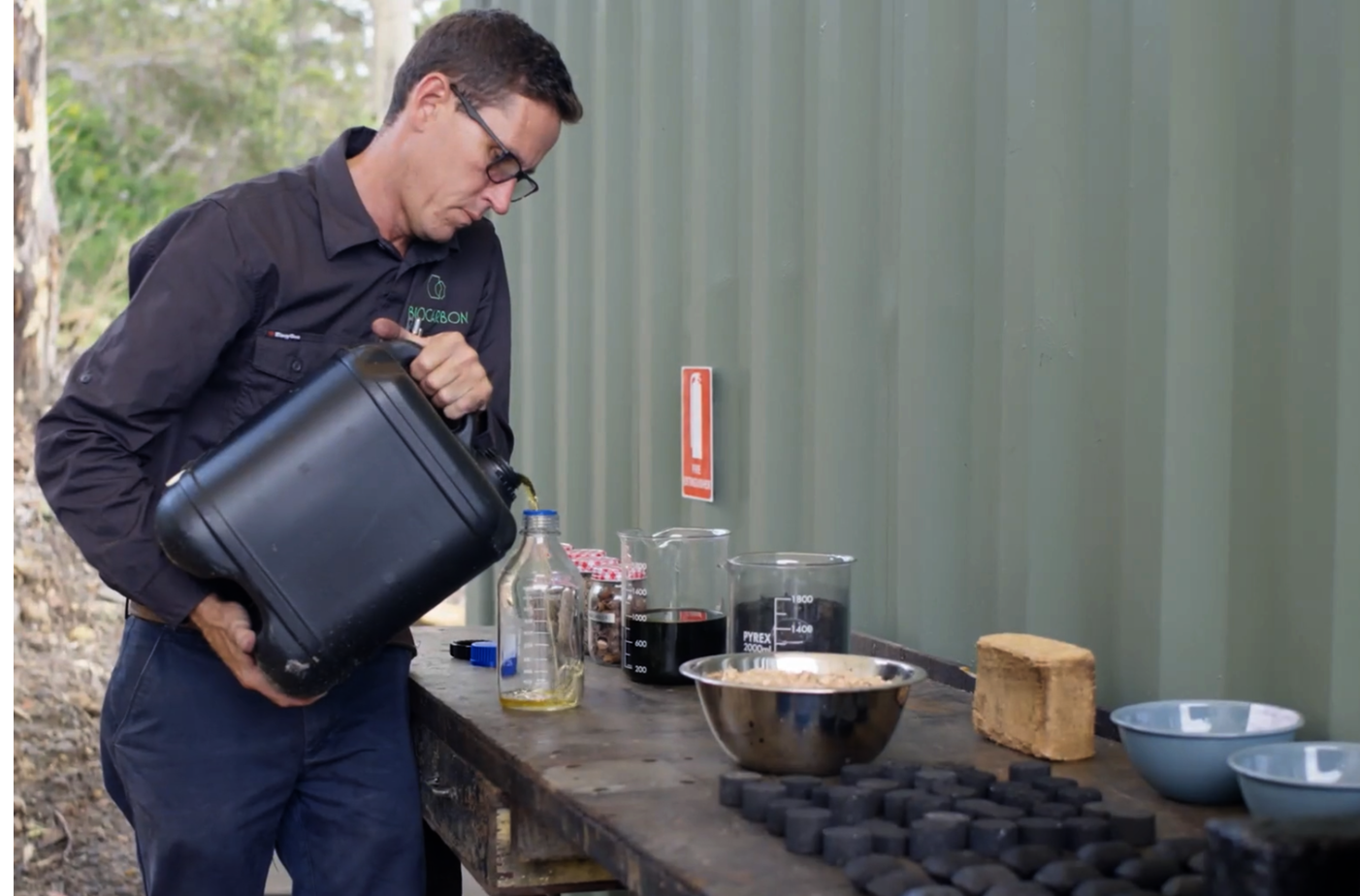
Future Prospects
Charcoal is poised to play a significant role in CO2 removal and the decarbonization of industries. The key challenges are to lower the cost of production and facilitate industry transition, which BioCarbonâs breakthrough technology is addressing.
â
For more information, visit BioCarbon.